Professional Advice on What is Porosity in Welding and Just How to Address It
Professional Advice on What is Porosity in Welding and Just How to Address It
Blog Article
Untangling the Enigma of Porosity in Welding: Tips for Decreasing Defects and Maximizing Quality
In the complex world of welding, porosity continues to be a persistent challenge that can significantly impact the high quality and honesty of bonded joints. Comprehending the elements that contribute to porosity formation is critical in the pursuit of flawless welds. By deciphering the mystery of porosity and executing efficient methods for problem reduction, welders can raise the criteria of their work to attain remarkable high quality outcomes. As we explore the midsts of porosity in welding, uncovering the secrets to its avoidance and control will certainly be paramount for professionals looking for to understand the art of high-grade weldments.
Recognizing Porosity in Welding
Porosity in welding, an usual problem encountered by welders, refers to the visibility of gas pockets or voids in the welded material, which can jeopardize the honesty and high quality of the weld. These gas pockets are usually entraped during the welding process as a result of different factors such as incorrect securing gas, polluted base products, or incorrect welding specifications. The development of porosity can deteriorate the weld, making it prone to fracturing and deterioration, ultimately resulting in architectural failings.
By identifying the relevance of preserving correct gas protecting, ensuring the cleanliness of base products, and optimizing welding settings, welders can significantly minimize the probability of porosity formation. On the whole, an extensive understanding of porosity in welding is necessary for welders to generate high-quality and durable welds.
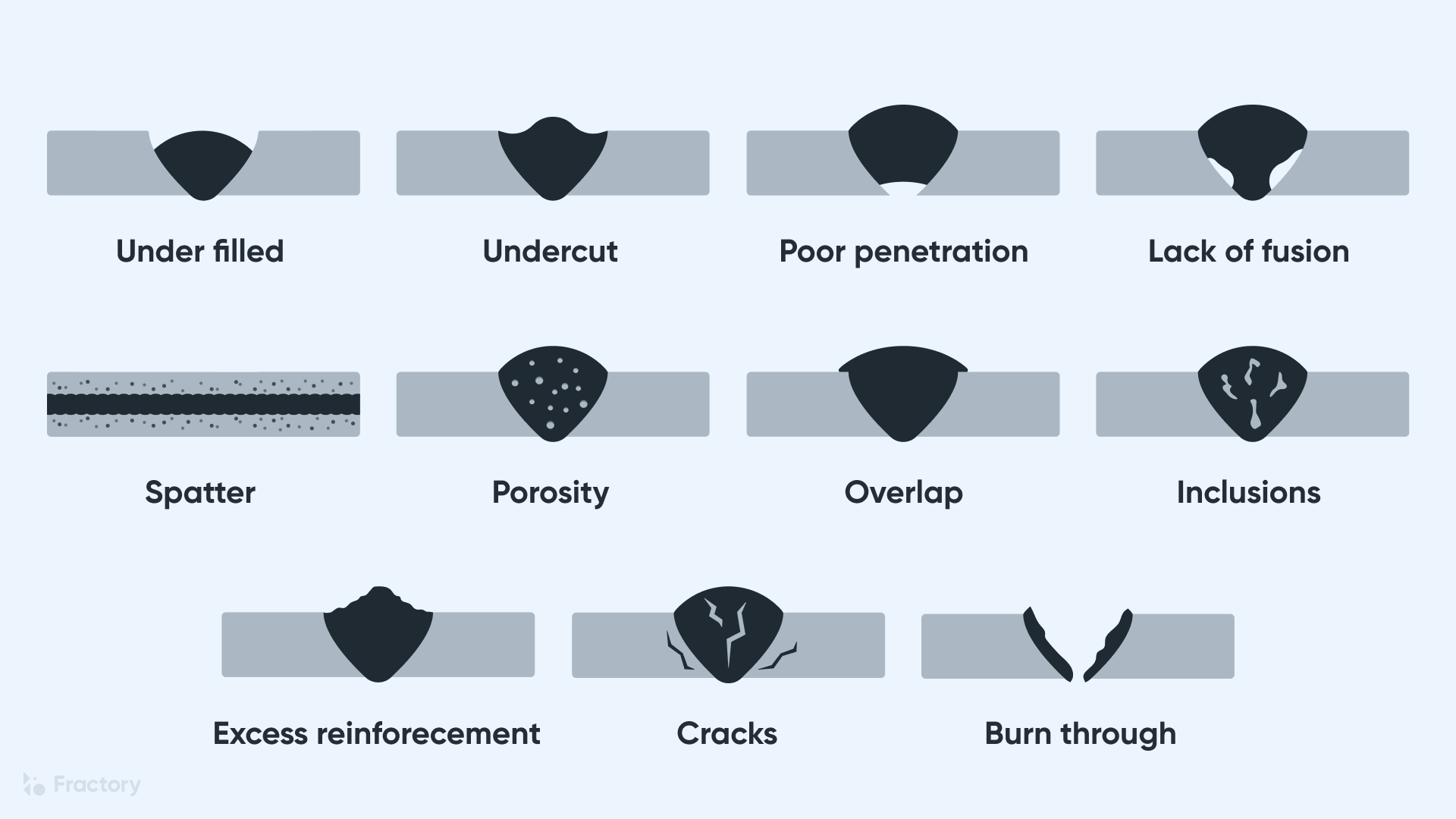
Common Sources Of Porosity
When evaluating welding procedures for possible high quality concerns, comprehending the common reasons of porosity is crucial for maintaining weld stability and protecting against structural failings. Porosity, characterized by the existence of tooth cavities or gaps in the weld steel, can dramatically compromise the mechanical residential or commercial properties of a welded joint.
Additionally, welding at improper specifications, such as exceedingly high travel rates or currents, can generate extreme disturbance in the weld swimming pool, trapping gases and creating porosity. By resolving these typical causes via appropriate gas protecting, material prep work, and adherence to ideal welding criteria, welders can lessen porosity and boost the top quality of their welds.
Techniques for Porosity Avoidance
Executing reliable preventative procedures is important in minimizing the incident of porosity in welding processes. One method for porosity avoidance is guaranteeing proper cleansing of the base steel before welding. Impurities such as oil, grease, corrosion, and paint can result in porosity, so complete cleansing using ideal solvents or mechanical methods is necessary.

Another trick safety net is the option of the right welding consumables. Utilizing premium filler products and protecting gases that are ideal for the base metal and welding process can dramatically lower the threat of porosity. In addition, maintaining appropriate welding criteria, such as voltage, present, take a trip rate, and gas flow price, is essential for porosity avoidance. Departing from the recommended setups can lead to inappropriate gas protection and inadequate combination, resulting in porosity.
Additionally, employing correct welding techniques, such as preserving a constant travel speed, electrode angle, her comment is here and arc length, can assist stop porosity (What is Porosity). Adequate training of welders to guarantee they adhere to best techniques and quality control procedures is additionally necessary in minimizing porosity issues in welding
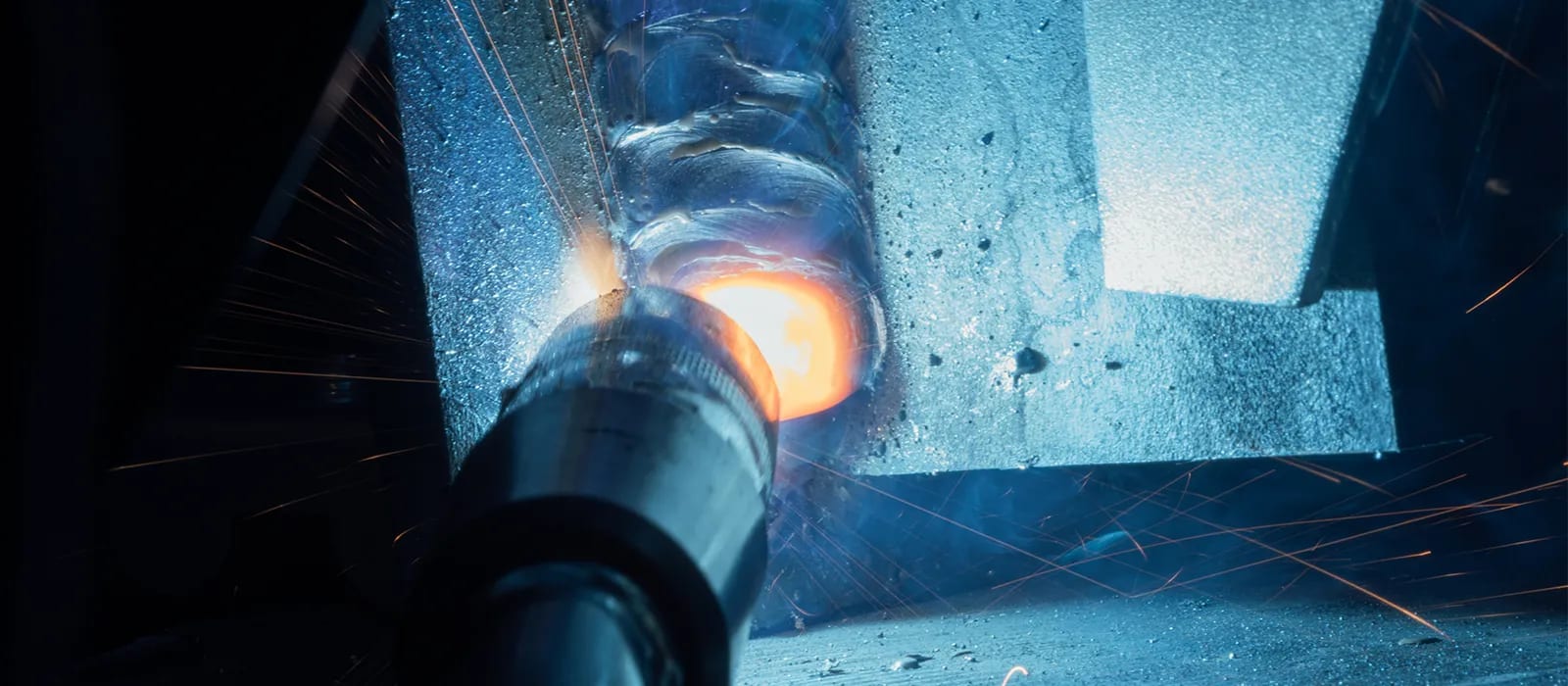
Best Practices for High Quality Welds
Guaranteeing adherence to sector standards and appropriate weld joint prep work are essential elements of attaining consistently premium welds. In addition to these fundamental actions, there are several finest methods that welders can implement to further improve the high quality of their welds. One key method is maintaining correct sanitation in the welding area. Contaminants such as oil, oil, corrosion, and paint can negatively affect the top quality of the weld, leading to issues. Completely cleansing the workpiece and surrounding location before welding can aid mitigate these problems.
One more best technique is to thoroughly choose the proper welding parameters for the specific materials being joined. Proper criterion option makes certain optimal weld penetration, fusion, and overall top quality. Making use of top quality welding consumables, such as electrodes and filler metals, can substantially influence the last weld top quality.
Importance of Porosity Control
Porosity control plays an important function in making certain the honesty and quality of welding joints. Porosity, characterized by the visibility of cavities or gaps within the weld metal, can substantially compromise the mechanical residential or commercial properties and structural stability of my latest blog post the weld. Extreme porosity weakens the weld, making it more prone to cracking, deterioration, and total failing under operational loads.
Effective porosity control is important for preserving the wanted mechanical buildings, such as stamina, ductility, and sturdiness, of the bonded joint. What is Porosity. By decreasing porosity, welders can boost the general quality and reliability of the weld, making certain that it satisfies the performance requirements of the intended application
Moreover, porosity control is essential for accomplishing the desired visual look of the weld. Too much porosity not only deteriorates the weld however also interferes with its visual appeal, which can be essential in markets where looks are essential. Appropriate porosity control methods, such as using the right protecting gas, regulating the welding parameters, and guaranteeing proper cleanliness of the base materials, are essential for generating high-quality welds with minimal defects.
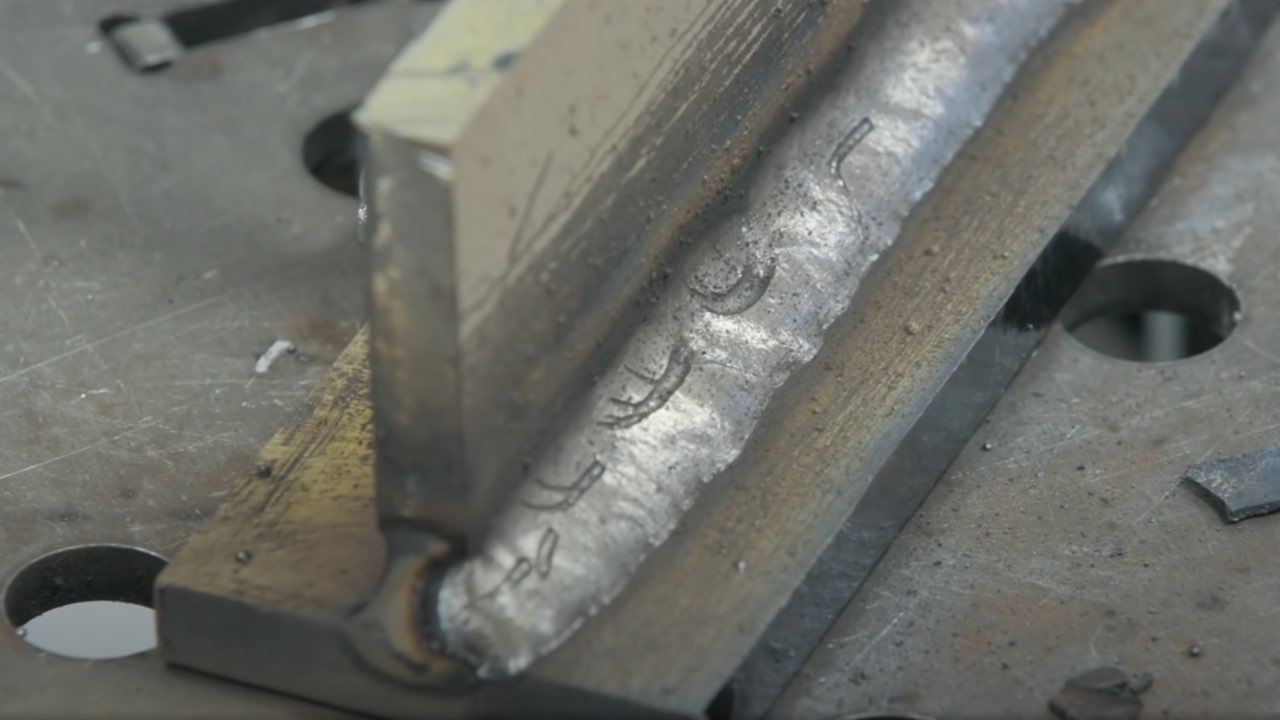
Conclusion
In verdict, porosity in welding is an usual pop over here issue that can jeopardize the top quality of the weld. It is essential to manage porosity in welding to guarantee the integrity and toughness of the final item.
Report this page